LDC GROUP Business case
Thimon installed a WRA-PAL SPILOTE TWIN high-speed spiral wrapping line at one of the LDC group's logistics platforms. Our machine fits in perfectly with the existing handling processes of the European leader in poultry and delicatessen dishes (LE GAULOIS, LOUÉ, MAITRE COQ, MARIE brands, etc.).The LDC teams are fully satisfied with the commissioning of this new machine, which has enabled them to achieve the expected level of productivity, while offering them prospects for future development.
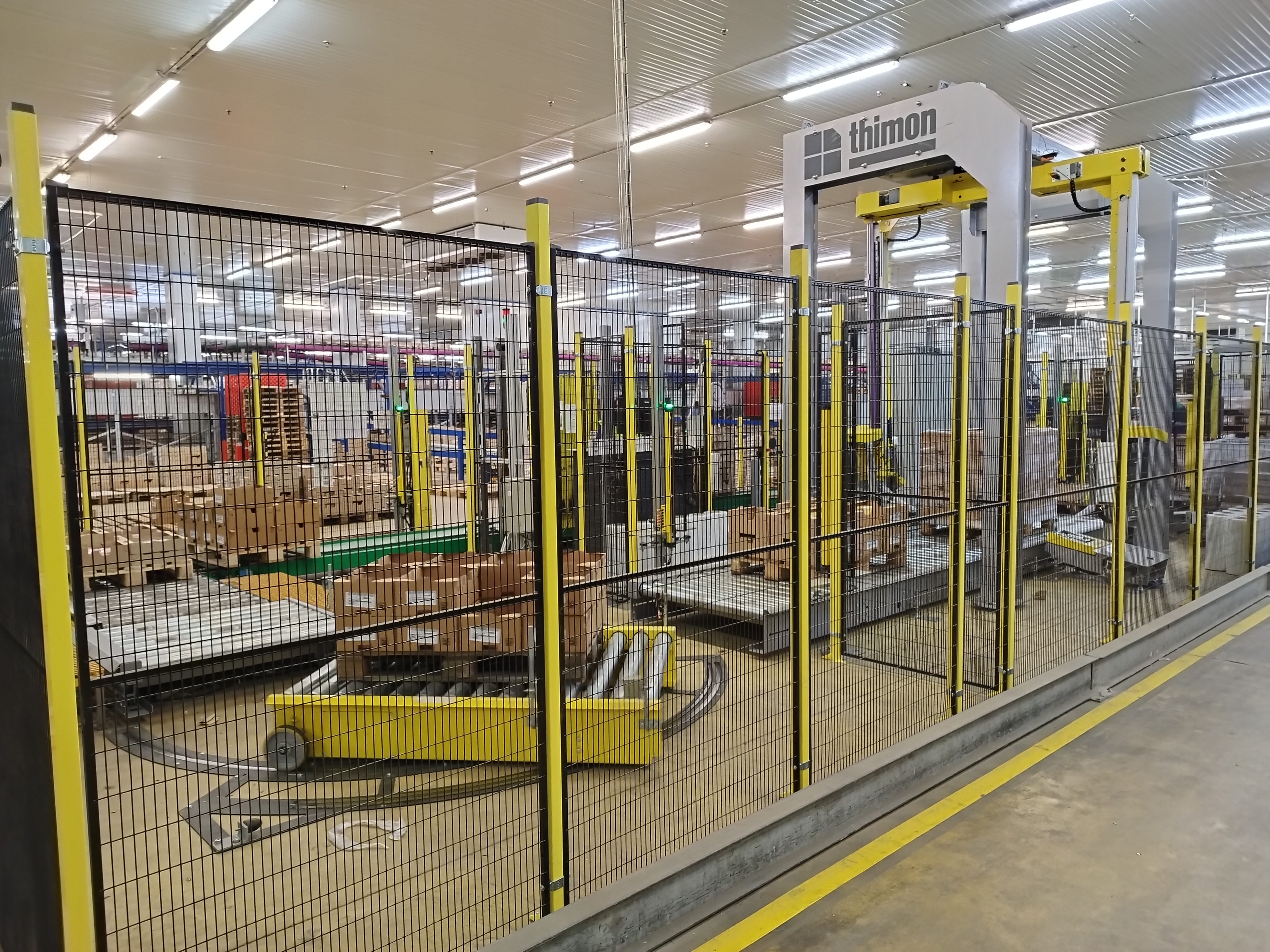
The customer's request
The site was already equipped with automatic wrapping machines, but these were showing signs of serious ageing, leading to repeated malfunctions that were detrimental to productivity.
The project presented a number of challenges, including:
- Installation in a small available space;
- Installation in a positive cold environment (0 - 5°C);
- Use and control of existing, third-party conveyor elements;
- Supplying pallets from multiple entry points and orientations;
- Adaptation to an existing upstream handling height that is different from the downstream handling height;
- Cohabitation of THIMON teams with an active site (no production stoppage).
The Thimon answer
Our teams seized the opportunity to meet these challenges by offering personalised support, as close as possible to the field and to the needs of the LDC teams, and by designing a tailor-made implementation, specifically adapted to the site's constraints.
Our proposal was therefore to deploy a WRA-PAL SPILOTE TWIN high-speed spiral wrapping solution, incorporating in particular:
- An automatic spiral wrapping machine with double rotating arms, capable of handling 100 pallets per hour, without compromising load stability;
- The reuse of existing handling elements, with a view to sustainable development;
- Tailor-made design of a revolving conveyor to take account of the limited space available and existing traffic flows;
- The use of motorised conveyors with a gradual gradient, to pick up pallets at ground level at the end of the line;
- Our didactic ‘THIMON OS VISION’ human-machine interface, providing line operators and maintenance staff with a highly intuitive user experience.
The result
Record time
for making this installation
Produ ctivity
expected level achieved
Film
Qualification and optimisation of stretch film consumption, thereby reducing the environmental footprint
"The success of this project is the fruit of an exemplary collaboration between our two teams, which we share with enthusiasm. This great adventure reflects our desire to cultivate lasting relationships, where the pride we feel in our customers matches the pride they feel in us.
At Thimon, we believe in exceeding expectations. More than just supplying packaging machinery, we're committed to providing customised solutions, listening carefully and, above all, delivering results that fully meet our customers' challenges. Each project becomes an exciting collaboration where the quest for excellence is our norm."
Yohann GAIDON, Managing Director at THIMON